Aluminum Extrusion Profile
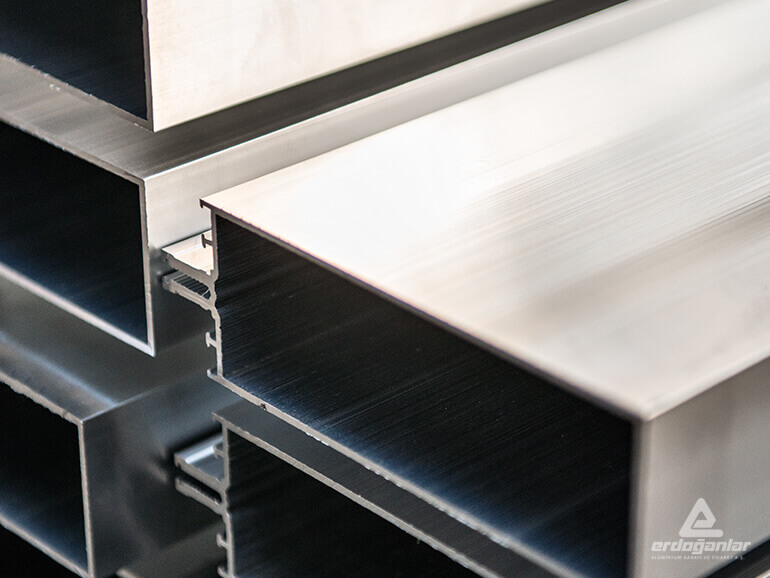
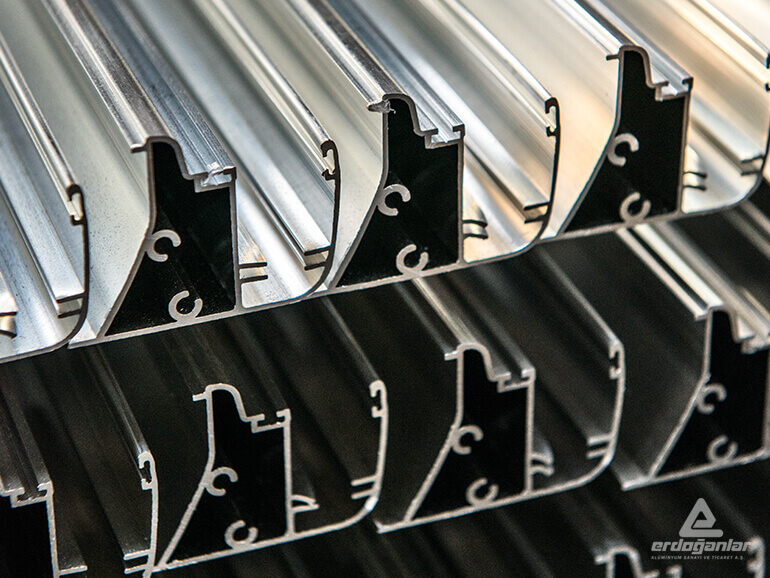
Aluminum extrusion is the process of transforming aluminum alloy into cross-sectional profiles. The end-results have a wide range of uses, and can be easily machined and cast yet offer strength and stability. While you do get custom aluminum extrusion shapes, there are three main types of aluminum extrusion profiles, each serving its own purpose for unique projects.
These profiles include hollow, semi-hollow, and solid extrusion profiles. In this blog, we’ll give you the low-down on the different types of aluminum extrusion profiles and what they’re commonly used for.
Solid aluminum extrusions have no voids or openings. These solid structures have a wide variety of uses, including creating compact, cross-sectional structures, structures with or without protrusions, curved shapes, wrap-around shapes, and more! This process is usually lower-priced due to the fact that it’s easier and faster to extrude.
Semi-hollow aluminum extrusions are only partially enclosed. A semi-hollow extrusion usually includes shapes that are circular or rectangular but require a gap on one side. This can become confusing as a solid shape can also include a partially enclosed void. The difference lies in the size of the respective gap.
Hollow Aluminum extrusions are shapes that are completely hollow anywhere in the cross-section. This means that the void or opening can include a specific shape, be molded into a variety of different shapes, or include more than one void extruded into a specific profile.
What Determines the Profile?
Examples of a solid extruded profile includes extruded rods, bars, and the like. Though a solid profile can also have a partially enclosed void, the semi-hollow structure is identified through the mathematical size of the gap. An example of a semi-hollow profile is a circular or rectangle structure with a gap in one side. A hollow profile is an extrusion that is completely enclosed with a void anywhere in the cross-section. Examples of hollow profiles include tubing and piping.
When designing the aluminum extrusion, there are five details to consider:
- Extrusion profile
- Tolerances
- Surface finish
- The type of alloy
- The circumscribing circle size
Good Profile Design Practices
There are various factors involved when deciding on the design of the aluminum extrusion profile. These characteristics must be followed to determine the quality of the end product. For example, you need to determine the thickness of the aluminum you’re using and compare it to the structural requirements. Then, try to ensure the thicknesses are as uniform as possible.
Specifying the Aluminum Thicknesses Before Extrusion
Whether the structure requires low or high stress areas, it’s always best to ensure the metal is just heavy enough to meet the requirements. Keeping the necessary thickness will avoid the risk of distortion and damage, while keeping the end product sturdy enough for use.
Keeping Thicknesses Uniform
While the extrusion process allows for the application of additional metal where necessary, it’s always best to avoid large differences between thick and thin areas as this can create dimensional control problems during extrusion. A tip when combining thick and thin dimensions, is to fade the transitions with a curve instead of a sharp angle.
Are you planning on creating your own aluminum extrusions? If you need custom aluminum extrusions, we can easily and effectively create high-quality solid, semi-hollow, and hollow aluminum extrusions to match your requirements.
Contact us today for more information.